Стекло
Стекло — материал, получаемый при остывании расплава в виде изотропного, хрупкого, прозрачного или просвечивающего тела и обладающий в результате постепенного увеличения вязкости механическими свойствами твёрдых тел. Процесс перехода из жидкого состояния в стеклообразное — обратимый. При нагревании стекло не плавится, а постепенно размягчается, переходя из твёрдого в тягучее и наконец в жидкое состояние; лишь при особых температурных условиях может кристаллизоваться.
Стекло
Стекло впервые было рождено огнём вулканов. Изверженная и застывшая лава превращалась в огромные массивы натурального стекла различных оттенков. Из него первобытный человек изготовлял наконечники стрел, ножи и т. п. Искусственное стекло начали вырабатывать 3—4 тысячи лет до н. э. в Египте. С древних времён развивалось стеклоделие в странах Ближнего Востока (Сирия, Финикия, Причерноморье) и в Китае. Примерно за 1200 лет до н. э. была известна техника прессования стекла. Переворот в технологии стеклоделия на рубеже нашей эры вызвало изобретение метода выдувания полых стеклянных изделий, широко применённого мастерами древнего Рима. В древнем же Риме впервые стекло было использовано в качестве оконного материала. В конце V века центр стеклоделия перемещается в Византию, а с XIII века мировым центром стеклоделия становится Венеция, где вырабатывались высоко художественные изделия из стекла (тончайшие декоративные сосуды разнообразных форм, туалетные зеркала, бисер, бусы и др., расписанные эмалями, покрытые золотом, цветными стеклянными нитями). В XVII веке возникают первые стекольные заводы в ряде стран Западной Европы. Широкого развития достигло стеклоделие в Германии, Франции, Чехословакии, Швейцарии и др. В России стеклоделие возникло в IX—X веках, но первые заводы (Воскресенский, Измайловский под Москвой) появились в XVII веке. В XVIII и XIX веках был создан ряд крупных стекольных заводов (Мальцевские, Бахметьевский, Дятьковский и др.). К 1913 г. в России насчитывалось 275 стекольных заводов, но производство оставалось в основном ручным, механизация вводилась очень медленно. Коренные изменения произошли в стекольной промышленности за годы Советской власти. Построены новые, полностью механизированные заводы, реконструированы и механизированы старые; освоено производство всех без исключения видов техники стекла.
Благодаря своим особым свойствам (термическая и химическая стойкость, светопрозрачность, исключительная способность к формованию, высокий коэффициент светопреломления и др.) стекло является очень ценным материалом для изготовления совершенно различных по назначению изделий (стеклянная посуда и различные виды стеклянной тары, зеркальное, оконное и полированное стекло, электролампы и радиоколбы, различные приборы, светофильтры, стеклянные блоки, облицовочные плиты, пеностекло, стекловата, стеклоткани, детали для оптических приборов и др.).
По назначению стекло подразделяется на оконное, посудное (сортовое), тарное, химико-лабораторное, термометрическое, строительное, оптическое, электровакуумное, зеркальное, стекловолокно и другие виды технического стекла. Каждый из этих видов стекла должен обладать своими особыми свойствами, зависящими от его химического состава, определяемого в основном вводимыми в стекло при его изготовлении окислами. В зависимости от природы главных стеклообразующих окислов промышленные стёкла делятся на силикатные, боросиликатные, боратные и фосфатные. Наиболее часто в составе промышленного стекла применяются окиси кремния, натрия, калия, кальция, магния, алюминия, бора и свинца.
Силикатные стекла имеют наибольшее распространение.
Применяются при изготовлении оконного и полированного стекла, консервной, парфюмерной и медицинской тары, столовой посуды и других изделий. В составе этих стекол содержится 60—75% окиси кремния; кроме того, вводятся окиси натрия калия, окислы кальция, магния, алюминия, свинца и др.
Стекло, в составе которого окись свинца достигает 15—30%, называется свинцовым хрусталём или просто хрусталём. Хрусталь отличается высоким показателем светопреломления, наибольшей прозрачностью и белизной, большим удельным весом; легко поддается шлифовке. Из хрусталя изготовляются лучшие сорта сортовой посуды, высококачественные художественные изделия и искусственные драгоценные камни.
К группе силикатных относится также большинство цветных и глушёных стекол, в состав которых добавляются красители и глушители, в частности сульфидное стекло. Цветные и глушёные стекла применяются для изготовления сортовой посуды, декоративных и светотехнических изделий (линзы, светофильтры, фонари).
Боросиликатные стёкла — стёкла, основными структурными окислами которых являются окись бора, кремнезём и глинозём. Обладают высокой термической и химической стойкостью и высокими оптическими свойствами. Применяются при изготовлении специальных стёкол для электровакуумной и оптической промышленности, химической и лабораторной посуды, части медицинской тары и стеклянного волокна.
Боросиликатное стекло с высоким содержанием глинозема и низким — щелочей применяется для изготовления бытовой жароупорной посуды (см.
Посуда стеклянная), химической посуды, электровакуумных баллонов, водомерных стекол и др.
Боратные стёкла — стёкла с окисью бора в качестве основного структурного окисла. Отличаются высокой устойчивостью против паров натрия. Применяются для изготовления целого ряда стекол специального назначения, в частности трубок накладного стекла для ламп с парами натрия.
Фосфатные стёкла — стёкла с окисью фосфора, как основным структурным окислом. Применяются для изготовления ряда изделий специального назначения, в частности смотровых окон и трубок для аппаратов в производстве стекол оптических и для легкоплавких эмалей.
Основной химический состав некоторых видов стекла
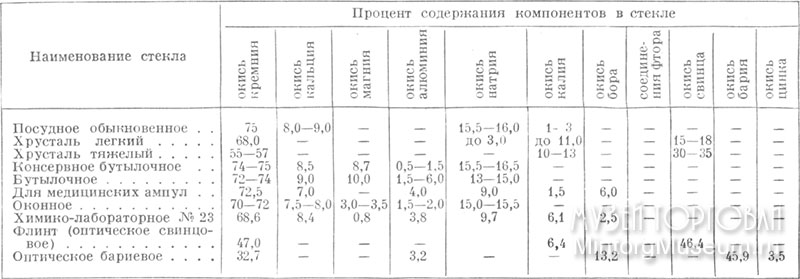
Производство стекла
Производство стекла состоит из двух основных процессов: подбор и подготовка соответствующих изготовляемому виду стекла сырьевых материалов и приготовление из них шихты; варка стекломассы, из которой вырабатываются стеклянные изделия.
Сырьевые материалы, идущие на изготовление стекла, делятся на основные (стеклообразующие) и вспомогательные.
Основные материалы — материалы, посредством которых в стекло вводятся кислотные, щелочные и щелочноземельные окислы, определяющие его физико-химические свойства. К ним относятся кремнезём, окись бора, окись алюминия, окись натрия, окись калия, окиси кальция и магния, окись бария, окись цинка, окись свинца и др.
Кремнезём вводится главным образом посредством кварцевого песка или кварца. В составе шихт большинства стекол содержится 60— 70% кварцевого песка. Качество кварцевого песка определяется содержанием основного вещества (окиси кремния) и примесей (окислов железа, титана, хрома и др.). Высокосортные кварцевые пески содержат до 98—99% окиси кремния. Наиболее вредными примесями являются закись и окись железа; незначительное их присутствие придаёт стеклу желтовато-зеленоватую окраску. Допускаемое содержание окислов железа в песке не должно превышать (в %): при изготовлении оптического стекла и хрусталя для посуды — 0,012; зеркального стекла — 0,05; стекла, предназначенного для аптекарской, химической и медицинской тары — 0,20; листового оконного стекла — 0,10; посудного стекла — 0,025; бутылочного полубелого стекла — 0,30 (для бутылочного тёмно-зелёного стекла не нормируется). Для изготовления стекла пригодны пески, в которых зёрна размером от 0,1 до 0,5 мм составляют не менее 85—90% Однородность величины зёрен обеспечивает их равномерное растворение при варке и ускоряет варку стекла.
Окись бора вводится в виде борной кислоты или буры; придаёт стеклу ряд ценных свойств: при замене окисью бора щелочных окислов снижается коэффициент расширения стекла, повышается его термическая и химическая устойчивость; увеличивается скорость варки стекла. Широко применяется для выработки термически стойких и специальных стекол, химической и лабораторной посуды.
Окись алюминия (глинозём) вводится с глиной, каолином и различными горными породами; наряду с кремнезёмом является основным компонентом для большинства промышленных стекол; снижает коэффициент расширения, повышает термическую и химическую стойкость, улучшает механическую прочность и повышает твёрдость стекла. Применяется при изготовлении стекла оконного, тарного, термометрического, стекла для жароупорной и химической посуды и других специальных стекол.
Окись натрия является важной составной частью большинства промышленных стекол. Стекломасса оконного и тарного стекол, сортовой посуды и ряда других изделий содержит от 13 до 16% окиси натрия. Вводится в состав стекла посредством кальцинированной соды, сульфата натрия, селитры.
Окись калия применяется главным образом в производстве высокосортной сортовой посуды, ряда цветных, оптических и технических стекол, хрусталя; заменяет окись натрия. Вводится с поташом, содовопоташной смесью и калиевой селитрой. Повышает вязкость и блеск стекла, значительно улучшает окраску цветных стекол. В присутствии окиси калия, например, окрашенные селеном стёкла приобретают приятный розовый оттенок.
Окиси кальция и магния также являются важными составными частями большинства промышленных стекол; окись кальция вводится в состав стекла посредством известняка, мела, иногда мрамора; окись магния — посредством доломита, магнезита. Окись кальция облегчает варку и осветление стекла и придаёт ему химическую устойчивость. Окись магния снижает способность стекла к кристаллизации.
Окись бария повышает блеск и увеличивает коэффициент преломления стекла; введение в состав стекла до 0,5% окиси бария ускоряет его варку. Вводится с углекислым, сернокислым и азотнокислым барием. Применяется для изготовления оптических и специальных стекол, а также высших сортов столовой посуды (баритовый хрусталь).
Окись цинка понижает коэффициент термического расширения стекла, делает его более устойчивым к резким изменениям температуры, повышает химическую устойчивость и увеличивает (по сравнению с окисью кальция) коэффициент преломления. Вводится с цинковыми белилами. Применяется преимущественно при изготовлении оптического, термометрического, лабораторного молочного и некоторых видов цветного стекла (селеновый рубин).
Окись свинца значительно повышает показатель преломления и удельный вес стекла. Свинцовое стекло легче поддаётся шлифовке, чем кальциевое. Вводится со свинцовым глетом и свинцовым суриком. Применяется главным образом в производстве оптического стекла, хрустальной посуды, искусственных драгоценных камней, эмалей.
Вспомогательные сырьевые материалы подразделяются на осветлители, обесцвечиватели, красители и глушители.
Осветлители вводятся в шихту для освобождения стекломассы от газообразных пузырьков, образующихся в процессе варки стекла. К ним принадлежат: калиевая и натриевая селитры, трёхокиси мышьяка и сурьмы, фтористые и аммониевые соли, хлористый натрий и в небольших количествах сульфат натрия. Эти вещества разлагаются при более высокой температуре с выделением газа, который, проходя через толщу стекломассы, захватывает все мелкие газообразные включения и уносит их.
Обесцвечиватели вводятся в состав стекла, чтобы уничтожить зеленоватый оттенок, получающийся от окислов железа, попадающих из сырьевых материалов и огнеупоров. Существует два способа обесцвечивания стекла — химический и физический.
Химический способ имеет назначением перевести закись железа (более интенсивный краситель) в менее интенсивный — окись железа. Полностью обесцветить стекло этим способом не удаётся. Для химического обесцвечивания применяются трёхокиси мышьяка и сурьмы, селитра и др.
Физический метод заключается в нейтрализации зелёных и жёлтых оттенков путём добавления в состав стекла незначительного количества красителей, окрашивающих стекло в цвет, дополнительный к зелёному. Для физического обесцвечивания применяются перекись марганца, селен, окись никеля, окись кобальта и редкоземельные элементы.
Красители вводятся в шихту для окрашивания стекла в различные цвета. К ним относятся: ряд соединений металлов (марганца, кобальта, никеля, хрома, железа, урана, меди, золота, серебра, кадмия), а также селен, сера и углерод. Окись марганца окрашивает стекло в фиолетовый цвет; закись кобальта — в синий (кобальтовый); соединения хрома — в изумрудно-зелёный; селен металлический — в розовый («розалии»); сернистый кадмий — в жёлтый; золото — в пурпурные цвета («золотой рубин») и т. д. Для получения переходных оттенков вводятся одновременно несколько красителей; так, например, смесь окиси урана с окисью меди даёт ярко-зелёные оттенки, окись урана с селеном окрашивает стекло в золотисто-янтарный цвет.
Глушители применяются для получения опалесцирующих, опаловых и молочных (рассеивающих свет) стекол. В качестве глушителей применяются соединения фтора, фосфора, олова, мышьяка и цинка. Наибольшее распространение имеют плавиковый шпат, кремне- фтористый натрий, креолит, а также сернистый цинк. При варке стекла глушители обычно растворяются, а при охлаждении выделяются в виде частиц, рассеивающих свет и делающих стекло малопрозрачным. В зависимости от степени заглушения различают стёкла молочные (наиболее заглушённые), опаловые (полупрозрачные) и опалесцирующие.
Подготовка сырьевых материалов и приготовление шихты
Подобранные в соответствии с видом изготовляемого стекла сырьевые материалы подвергаются тщательной обработке: обогащается песок (понижение содержания вредных примесей путём промывки, магнитной сепарации и пр.); сушатся и размалываются мел и известняк; просеиваются на специальных ситах все камневидные материалы. Подготовленные таким образом основные сырьевые материалы, взятые в определённой пропорции в зависимости от химического состава стекла, смешивают и получают шихту. В неё добавляют соответствующие виду изготовляемого стекла вспомогательные материалы. Для улучшения качества и ускорения варки стекла перед засыпкой шихты в печь её тщательно перемешивают в механических смесителях. Наибольшая однородность шихты достигается при её брикетировании, которое исключает расслоение шихты при передвижении и уменьшает разъедание огнеупоров в печах. Для ускорения плавления шихты в неё добавляют стеклянный бой, который расплавляется раньше других компонентов.
Варка стекломассы
Варка стекломассы производится в стекловарных печах периодического (горшковые) или непрерывного (ванные) действия при температуре 1350—1600° (в зависимости от состава стекла). Ванные печи более производительны, чем горшковые, но в них можно варить одновременно только стекла одного состава, в то время как в горшковых — стекло разных составов. Варка различных стекол имеет ряд особенностей: варку стекла, содержащего большое количество соединений фтора (молочное или опаловое), ведут при более низких температурах (1300—1350°), а стекло, содержащего повышенное количество окиси алюминия, — при более высоких (1500—1550°); всё стекло, содержащие окись свинца, во избежание его восстановления до металлического свинца, окрашивающего стекло в серый или коричневый цвет, — в окислительных условиях; такие стёкла, как медный рубин, требуют восстановительного режима варки (для выделения из закиси меди коллоидной металлической меди, окрашивающей стекло в красный цвет). В современных стекловаренных печах процессы, связанные с варкой, в значительной мере автоматизированы и поддаются строгому контролю.
Изготовление стеклянных изделий
Изготовление изделий из стекломассы состоит из формования изделий, постепенного их охлаждения, отжига или закалки и обработки изделий.
Формование производится различными способами. Основные из них: прессование, выдувание, прессовыдувание, вытягивание и прокатка.
Прессование — метод формования, при котором стекломасса, попадая в специальную форму пресса (матрицу), движением формующего устройства (пуансона) заполняет её. Применяются как ручные, так и автоматические прессы. Производительность автоматических прессов достигает при выработке мелких изделий (типа чайных стаканов) 40 тысяч штук в сутки. Прессованием обычно получают изделия несложной конфигурации. Изделия с тонкими стенками, большой высоты или сложных форм прессованием получить трудно, т. к. стекломасса быстро охлаждается и становится хрупкой прежде, чем заканчивается процесс формования. Методом прессования вырабатываются многие виды столовой посуды, отдельные виды стеклянной тары, стеклянные изоляторы, ролики и др.
Выдувание — оригинальный способ формования. Широко распространён, в особенности при изготовлении полых изделий различной формы и размеров. При этом способе стекломасса приобретает определённую форму с помощью сжатого воздуха от компрессора или воздуха, вдуваемого рабочим-стеклодувом. Выдуванием вырабатываются: бутылки; консервная, парфюмерная и медицинская тара; столовая посуда; электроосветительное стекло и др. Часть столовой посуды выдувается вручную при помощи стеклодувной трубки; часть бутылок парфюмерной и аптекарской тары — на полуавтоматах; большинство же изделий к 60-м годам производилось — на высокопроизводительных автоматах 2ЛАМ, ВВМ-Ю, ВС-24, АВ-4 и др., достигающих при изготовлении чайных стаканов производительности 35 тысяч штук в сутки, а при выработке парфюмерной и аптекарской посуды — 50 тысяч штук в сутки.
Прессовыдувание применяется при производстве посуды и широкогорлой тары. Предварительная заготовка («баночка») и формование горла изделия производятся прессованием (в черновой форме), а остальные процессы — выдуванием (в чистовой форме).
Вытягивание применяется при изготовлении оконного и технического листового стекла, труб, стержней, дротов и стеклянного волокна. Вытягивание оконного стекла производится машинами Фурко, стеклянной ленты разной ширины — серией парных асбестовых валиков.
Прокатка применяется для изготовления преимущественно строительного (толщиной 3 мм и больше), узорчатого и армированного (с закатанной в него металлической сеткой) стекла. При прокатке стекломасса непрерывно поступает струёй из печи в пространство между вращающимися вальцами, где и формуется в ленту, убираемую транспортёром, либо выливается на плоскость, где подвергается давлению катящегося вала.
Отжиг
Отжиг производится для уничтожения внутренних неравномерных напряжений, возникающих при быстром охлаждении в процессе формования и вызывающих самопроизвольное растрескивание изделий. При отжиге изделия выдерживаются в специальных печах в течение определённого времени при температуре, близкой к температуре размягчения стекла (для большинства стекла 500—560°), а затем медленно охлаждаются по определённому режиму. Длительность отжига определяется толщиной изделий и составом стекле и колеблется в пределах от нескольких минут (оконное стекло) до нескольких месяцев (астрономические объективы). Отжиг производится в отжигательных печах непрерывного или периодического действия.
Закалка
Закалка отформованных изделий — операция, противоположная отжигу. Закалённые изделия термически и механически значительно прочнее отожжённых. В результате закалки оконного стекла получается не бьющееся стекло (так называемый сталинит), применяемое для осте¬кления окон вагонов, самолетов, автомобилей. Закалке могут также подвергаться полые из¬делия (столовая посуда, консервная тара). При закалке изделие равномерно разогревает¬ся до темп-ры, близкой к размягчению, а затем быстро охлаждается путем равномер¬ного обдувания воздухом или погружаются в масляную среду. После формования и отжига (или закалки) большая часть изделий подвергается обра ботке.
Обработка стекла
Обработка стеклянных изделий делится на горячую (огневую), холодную (механическую) и химическую, которые применяются как в отдельности, так и в сочетании друг с другом.
Горячая обработка применяется для отколки колпачков, отопки края, огневой полировки и других операций, требующих нагревания изделий. Чтобы отделить колпачок, образующийся на выдувных изделиях после выработки в форме, на корпусе изделия наносят алмазом черту и направляют на неё острое пламя газовой горелки; колпачок отскакивает, образовавшийся неровный острый край шлифуется или подвергается так называемой отопке (оплавлению) вручную с помощью горелки или на машинах периодического или непрерывного действия, производительность которых, например при изготовлении стаканов, достигает 70—75 тысяч штук в сутки.
Холодная обработка включает резание (абразивным инструментом и циркульными пилами с алмазной набивкой), сверление (стальным сверлом с применением смачивающей жидкости, в состав которой вводится алмазный порошок), шлифование и полирование, а также гравирование.
Шлифование плоского стекла в большинстве случаев осуществляется с помощью порошкообразных крупнозернистых абразивов (обычно кварцевых песков) металлическими дисками (шлифовальниками). Для придания шлифованной поверхности прозрачности и блеска стекла полируется. Полирование производится на таких же станках, что и шлифование. В качестве абразива применяются тонкозернистые материалы (обычно крокус), а металлический шлифовальник заменяется войлочным кругом В производстве столовой посуды также применяется шлифование, с помощью которого наносятся различные рисунки (так называемая алмазная грань); производится это абразивными инструментами (шлифовальные круги из карборунда и олунда). Полирование столовой посуды производится щётками из морской травы или химическим путём (смесью плавиковой и серной кислот). Гравирование изделий обычно производится небольшими медными колёсами с помощью тонкого наждачного порошка, мелкими абразивными кругами или с помощью ультразвука. Последний метод позволяет наносить любые сложные и тонкие рисунки. При поточном производстве шлифовка и полировка производятся на конвейерных линиях. Химическая обработка стекла применяется для получения матовой рассеивающей свет поверхности, а также кислотной полировки, клеймения и художественно-декоративной отделки стеклянных изделий. Наиболее распространённым видом химической обработки является травление стекла газообразным фтористым водородом или растворами плавиковой кислоты и её солей, с добавлением др. химических веществ, которые растворяют стекло, причём образуются нерастворимые или мало растворимые соли кальция, магния и натрия, отлагающиеся на поверхности стекла, придавая ей матовость.
Кислотная полировка производится составом из растворов плавиковой кислоты в смеси с концентрированной серной кислотой; процесс полировки создает равномерное растворение шероховатостей на поверхности стекла, которая становится гладкой и блестящей.
Травление широко применяется для художественной обработки столовой посуды. Для нанесения методом травления тонких линейных рисунков применяются специальные машины — гильоширные и пантографы, резец которых вычерчивает рисунок на предварительно нанесённом на изделие защитном воскообразном слое, снимая его; после этого изделия погружаются в ванну с раствором кислот, которые протравливают стекло в местах, где оно обнажено резцом.
Одной из форм химической обработки стекла является иризация — обработка поверхности стекла парами хлористого олова и четырёххлористого титана в сочетании с другими солями. Поверхность стекла при этом покрывается тонкой интерфорирующей плёнкой, похожей на перламутр.
Широкое применение в декорировании сортовой посуды получило нанесение рисунков и покрытий ручным или механизированным способом препаратов жидкого золота, люстров, декалькомании (переводных картинок) и цветных силикатных красок, закрепляемых на изделиях специальным обжигом (см.
Посуда стеклянная) .
Классификация изделий из стекла
Из стекла вырабатывается чрезвычайно широкий ассортимент изделий, включающий следующие основные группы: сортовая и хозяйственная посуда, листовое оконное стекло, полированное стекло, стеклянные трубы, стеклянные блоки и другие виды строительного стекла, тарное стекло (бутылки, консервные банки, парфюмерные флаконы, аптекарская посуда), оптическое стекло, электровакуумное стекло (электроколбы, дрот и др.), светотехническое стекло (электроосветительная арматура, линзы, светофильтры, фары, сигнальное стекло для транспорта и пр.), безопасные стёкла (сталинит, трёхслойное), стеклянное волокно (стекловата, стеклолента, стеклонить и пр.) и пеностекло.
Описание изделий из стекла — Абажуры, Банки консервные, Блюда декоративные, Блюда столовые, Блюдца, Бокалы стеклянные, Бокальчики стеклянные, Вазочки столовые, Вазы для цветов, Вазы столовые, Вата минеральная, Глазные ванны, Глазные лопатки, Глазные пипетки, Горчичницы, Графины, Грудные накладки, Кастрюли, Кружки для хрена, Кружки пивные, Кружки Эсмарха, Крынка, Кубок призовой, Лабораторная посуда, Ламповые стёкла, Лампы керосиновые, Лампы медицинские, Лампы электрические, Лампы фотографические, Линза для телевизоров, Лупа, Лупа препаровальная, Маслёнки столовые, Молокоотсосы, Молочники, Наконечники стеклянные, Опарница, Очки, Пепельницы, Плевательницы, Подстаканники, Полоскательницы, Полочки туалетные, Посуда стеклянная, Пуговицы, Розетки для варенья, Рюмки, Салатницы, Сахарницы, Сливочники, Солонки, Соусники, Стаканы, Стаканы мерные, Стаканы туалетные. Стекло листовое, Стеклянная тара, Сухарницы, Тарелки столовые. Флаконы туалетные, Фужеры, Хренница, Хрусталь, Художественные изделия из стекла, Чайники столовые, Чайницы, Чашки.
Требования к качеству стекла
Назначение, конструкция и условия эксплуатации изделий из стекла чрезвычайно различны. В связи с этим стекло должно обладать не одним каким-либо определённым свойством, а сочетанием различных свойств. Это достигается в процессе изготовления стекломассы путём подбора соответствующих основных и вспомогательных материалов. Основные требования, предъявляемые к качеству стекла, относятся к внешнему виду, механической прочности, химической устойчивости против воздействия влаги, кислот, щелочей и других химических реагентов, термической устойчивости, светопреломлению и др. Основные дефекты стекломассы, отрицательно влияющие на качество изделий, следующие: разнотонность; камни — посторонние включения (частички огнеупоров или шихты), снижающие термостойкость стекла; шлиры — сгустки в виде бугорков, обычно с волнистыми ответвлениями; свили — волнистые полосы; пузыри — газообразные включения прозрачные и замутнённые (щелочной пузырь) диаметром свыше 0,8 мм; мошка — мелкие пузырьки диаметром до 0,8 мм; рух — закристаллизовавшиеся непрозрачные частицы стекла.
Требования к качеству, сортность каждого вида стеклянных изделий предусмотрены ГОСТ и ТУ на эти изделия.
Посуда стеклянная
Стекло листовое
Стекло настольное
Стеклорезы